iPhones India: Apple plans to shift iPhone production for US sales from China to India in response to new tariff measures.
- Key Point 1: Apple will manufacture most iPhones for the US in India, aiming to reduce the impact of tariffs.
- Key Point 2: Tim Cook confirmed that Vietnam and China will remain significant production hubs for other product lines.
- Key Point 3: The tariff-related cost impact for Apple is estimated at $900 million for the coming quarter.
- Key Point 4: US buyers are preemptively purchasing iPhones and other products to avoid potential price increases.
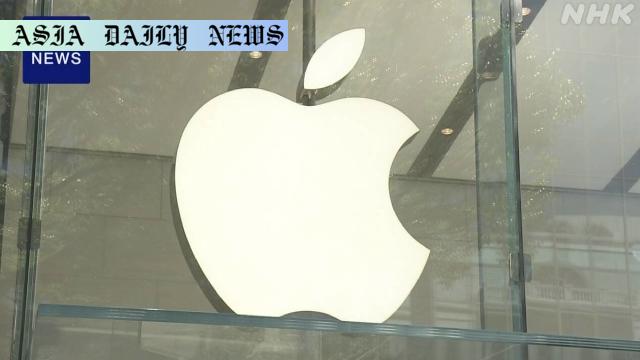
Apple’s Strategic Production Shift to India
Apple Inc., one of the technology world’s most influential firms, is pivoting a significant component of its manufacturing strategy to India. This bold move reflects an adaptive response to changing global trade dynamics, particularly in light of tariff measures introduced by the US government. According to Apple’s CEO Tim Cook, a majority of iPhones sold in the United States by the middle of this year will be produced in India. This decision stems primarily from the company’s attempt to minimize the financial burden imposed by new tariff policies.
India’s growing manufacturing capabilities, combined with favorable government reforms to attract foreign investments, have positioned the country as a viable production alternative to China. This shift underscores Apple’s effort to diversify its supply chain amid trade tensions and risks. Moreover, Cook highlighted that while iPhones for US consumers would increasingly originate from India, Vietnam and China would still play crucial roles in producing iPads and several other Apple products.
Breaking Down Apple’s Recent Financial Results
Alongside this landmark production announcement, Apple released its business performance for the January-to-March quarter, revealing solid growth. The company recorded an impressive $95.36 billion in total net sales, reflecting a 5% increase compared to the same quarter last year. Net income stood at $24.78 billion, marking a year-on-year growth of 4.8%. Analysts attribute this year’s robust sales performance partially to US consumers rushing to purchase iPhones and other products in anticipation of potential price hikes due to forthcoming import tariffs.
Remarkably, Apple’s ability to sustain growth during a time when many global firms face shrinking sales is worth noting. Diversification of production sites as a strategy positions the company to continue meeting consumer demand while remaining cost competitive even amid policy shifts. However, Cook admitted that the exact economic implications of tariffs and production transitions remain complex and difficult to quantify at this stage.
Cost Implications and Global Impact of Apple’s Move
Incorporating India as the primary production hub for US iPhones is expected to bring both opportunities and challenges. On the one hand, Apple could take advantage of lower production costs and geographical diversification, insulating itself from over-reliance on a single country like China. On the other hand, the transition entails significant short-term costs. Cook estimated that tariffs alone could add $900 million to Apple’s costs for the upcoming June quarter.
This shift in production will also profoundly influence the global supply chain ecosystem. Countries like India and Vietnam are likely to benefit economically, creating jobs and boosting local economies. Simultaneously, China will likely remain a vital partner for Apple, supplying a significant share of products sold outside the US market. Going forward, this strategy could pave the way for more companies to reevaluate their manufacturing dependencies and look for further diversification.
Future Implications for the Tech Industry
Apple’s decision carries broader implications for the technology industry and the global economy. The company’s reliance on India signals a shift in the global manufacturing landscape. As companies seek to mitigate geopolitical and economic risks, developing regions are increasingly likely to attract investments. The tech giant’s move may set a precedent, encouraging other multinational corporations to reconsider their dependencies on traditional hubs like China.
However, this strategic pivot is not without its hurdles. Governments and companies must work collaboratively to address concerns such as infrastructure limitations, regulatory challenges, and labor skill gaps in emerging markets. For Apple, the pursuit of cost efficiency and supply chain resilience will shape its global operations in the years to come.
Conclusion
Apple’s decision marks a transformative moment in the company’s history and reflects the broader trends shaping the global economy today. By leveraging India and Vietnam for its production needs, Apple aims to reduce its exposure to geopolitical risks and cost pressures. Time will reveal how this bold move impacts the company’s growth trajectory, brand value, and financial sustainability. For now, the shift stands as an indication of the changing tides in global trade and economics.
Commentary
Apple’s Strategic Move: Diversification and Its Implications
Apple’s decision to shift iPhone production for the US market to India is both timely and strategic. By doing so, the tech giant showcases its adeptness at navigating complex global trade challenges. The new tariffs imposed by the US administration posed a significant hurdle, and Apple has responded by diversifying its supply chain to mitigate the financial risks associated with such policies. Not only does this move strengthen Apple’s foothold in India, but it also underscores a larger trend toward diversification of manufacturing hubs.
India, in recent years, has positioned itself as an attractive destination for global tech manufacturing. The country’s steady advances in infrastructure development, coupled with favorable policies for foreign investments, have made it a viable alternative to China. Apple’s investment here will undoubtedly contribute to strengthening India’s reputation as a global manufacturing hub. Over time, this could also create a ripple effect, attracting similar investments from other industry giants and nurturing local talent in the process.
The Challenges of Transitioning to a New Manufacturing Hub
While Apple’s move is ambitious, it comes with its set of challenges. Transitioning production from China to India will require substantial logistical effort, training, and investment. Ensuring that Indian facilities maintain uniform quality standards comparable to those of Chinese operations would be crucial. Any hiccups in production could potentially impact Apple’s brand image and customer trust.
Moreover, while India has proven itself as a rising star in tech manufacturing, infrastructure development and regulatory barriers still need attention. It will be interesting to see how the Indian government and Apple work together to navigate these hurdles and ensure the seamless implementation of this production shift.
What This Means for Global Trade and the Consumer Market
On a broader scale, Apple’s decision signals an important lesson in supply chain resilience and adaptation. Geopolitical tensions between the US and China have encouraged multinational corporations to rethink their dependency on specific regions. By adopting a diversified manufacturing strategy, Apple reduces risks and ensures its ability to maintain supply chains despite policy changes. This move could potentially encourage other companies to follow suit, signaling profound shifts in global trade patterns.
All in all, Apple’s decision reflects its ability to balance global dynamics while prioritizing quality, cost-efficiency, and innovation. The coming years will likely reveal the full impact of this choice, not only on Apple but also on the tech industry and global economy as a whole.