Tariff: Honda and Nissan adjust US production plans to address Trump’s 25% tariff on automobiles, impacting their strategies.
Honda to transfer sedan production to Indiana due to tariffs.
Nissan reverts plan, retains Tennessee production cutbacks in Japan.
Automakers face logistical challenges with US-based operations.
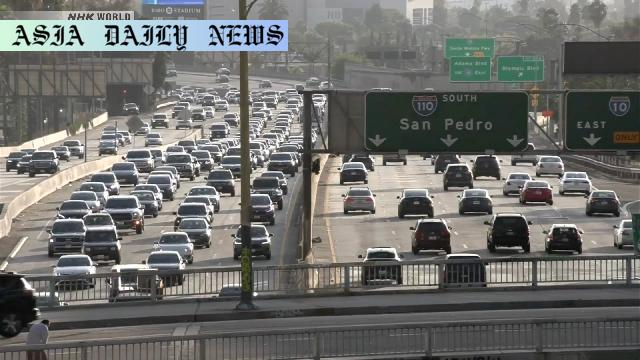
Addressing Challenges Arising from Tariff Policies
The automotive sector has once again proven its resilience as Honda Motor and Nissan Motor navigate the challenging terrains of international trade policies. The Trump administration’s imposition of an additional 25% tariff on automobiles has compelled these major automakers to make strategic adjustments in their production and distribution networks. These changes highlight the growing complexities multinational companies face in balancing profit margins with global trade policy fluctuations.
In a strategic move to reduce the financial impact of these tariffs, Honda has chosen to shift the production of its sedan vehicles from Japan to the U.S. Indiana facility. This relocation aims to not just mitigate tariff effects but cater effectively to a geographically advantageous supply chain within domestic markets. Indiana is set to become a significant production hub for Honda’s hybrid model, which currently produces 1,500 units monthly in Japan’s Saitama Prefecture. The cessation of production in Japan, projected by mid-year, aligns with Honda’s efforts to streamline operations and lower shipping costs.
Nissan, on the other hand, has opted for a slightly different approach. While the company maintains planned production levels in Tennessee, it announced a reduction of its sport utility vehicle output in Japan’s Fukuoka Prefecture. This reduction, expected to lower output by 10,000 units over three months, underlines the cost-saving measures being implemented to balance production costs amid increased tariffs. These strategies showcase the flexibility and resource optimization efforts of automakers under challenging trade conditions.
Strategic Relocation as a Key Response
Honda and Nissan have long relied on international operations to fulfill market demands, but the current tariff policies have forced them to rethink traditional approaches. By aligning production facilities closer to their target markets, these companies aim to better cater to local customer needs while avoiding excessive costs associated with exports. Honda’s shift to Indiana capitalizes on existing U.S. resources, including a highly skilled workforce and cost-effective transportation networks.
Nissan retains its commitment to domestic production within the U.S., with the Tennessee plant maintaining output levels and serving as a cornerstone for its American operations. However, the reduction in Japanese production indicates the heavy burden tariffs impose on automakers, necessitating local strategies to sustain profitability. This shift also reinforces the growing emphasis on solidifying regional supply chains versus relying heavily on global networks that may be disrupted due to policy changes or unexpected trade barriers.
Despite their proactive measures, both companies face challenges in expanding U.S.-based operations. Securing supply chains, ensuring a steady flow of essential automotive parts, and managing heightened production demand are just a few of the hurdles they face. These obstacles underscore not only the linear impact of tariffs but also the ripple effects across operational and logistical networks globally.
Broader Implications on the Industry
The strategies employed by Honda and Nissan could serve as a model for other automakers grappling with the implications of the U.S. automotive tariff. The ripple effects extend beyond the automotive sector, influencing ancillary industries, workforce dynamics, and even consumer pricing. The automotive industry’s shift toward regional production underscores the increasing need for robust supply chain management and effective cost control measures.
Automakers have long been regarded as an integral part of economic growth in their respective countries. Shifts in production locations impact employment rates, regional economic contributions, and global competition. Indiana, set to benefit from Honda’s new production footprint, will likely see an increase in employment opportunities and a boost in the state’s economy. On the other hand, reduced production in Japan could result in economic shifts, though these will likely be mitigated by diversification of operations within Honda’s and Nissan’s expansive global footprint.
Looking ahead, these adjustments are an apt reflection of how global trade dynamics influence industrial strategies. With tariffs and global supply chain disruptions becoming significant hurdles for automakers, businesses might be propelled to invest further in innovations that localize their operations and increase cost efficiency. These trends may also contribute to enhanced bilateral trade negotiations aimed at balancing economic interests and fostering stable international relations.
Commentary
The Importance of Strategic Flexibility
Honda and Nissan’s recent adjustments stand as a prime example of how organizations must adapt to external forces beyond their control. The imposition of a 25% auto tariff by the Trump administration has brought about challenges, not just for automakers but for the entire ecosystem surrounding the automotive industry. These challenges highlight the pivotal role strategic flexibility plays in tackling abrupt changes in trade policies and economic landscapes.
Honda’s decision to transfer production from Japan to Indiana showcases the company’s proactive approach to streamlining its operations. Tariffs of this magnitude can significantly dent profit margins, but by relocating production, Honda minimizes excessive shipping and tariff costs while simultaneously expanding its local presence. In addition, the move could yield a positive cross-industry ripple effect, from generating additional employment to bolstering local suppliers’ profitability. Each of these actions signifies Honda’s unwavering commitment to staying competitive in the American market.
The Implications of Global Localization
While Nissan has maintained its Tennessee operations after initially considering production cuts, its decision to scale down output in Japan speaks volumes about the long-term strategy automakers are considering. The delicate balance between regionalizing production and maintaining domestic operations remains a challenge. Companies must not only assess immediate benefits but also long-term sustainability and operational feasibility. For Nissan, this reduction highlights just how much trade policies can dictate large-scale decisions for global corporations.
However, localizing production is not without its challenges. The ripple effect extends to logistics, workforce training, and even environmental considerations. As automakers explore the feasibility of increasing production closer to target markets, they must overcome supply chain complexities to maintain efficiency without inflating costs unnecessarily. Both Honda and Nissan demonstrate resilience and adaptability under evolving circumstances, paving the way for innovation in their operational strategies under trade-related pressures.